The Nuts and Bolts of DOD Inventory Management

(Excerpted from GAO-14-495)
- DLA disposed of over $855 million in inventory that was more cost-effective to keep since it may be needed later. Why did it do this? DLA was trying to meet an internal goal that was not supported by economic analyses.
- The Air Force has retained over $2.6 billion in inventory without proper justification and without following DOD guidance. Although this could cost the Air Force in unnecessary storage expenses, it currently has no plans to review this inventory until the end of fiscal year 2016.
- The Army, Navy, and DLA don’t fully monitor inventory orders to prevent purchasing and storing unneeded items. For example, Navy management didn’t adequately review retention decisions, potentially resulting in the storage of excess inventory, and DLA wasn’t tracking and reviewing the reasons why excess orders weren’t cancelled, limiting its understanding of those orders.
- Questions on the content of this post? Contact Zina Merritt at MerrittZ@gao.gov.
- Comments on GAO’s WatchBlog? Contact blog@gao.gov.
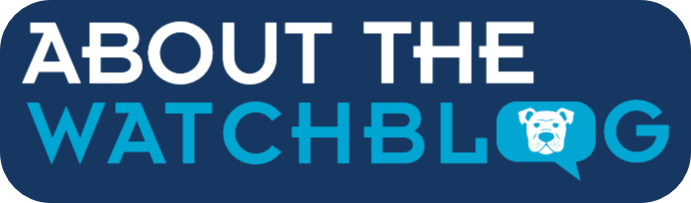
GAO's mission is to provide Congress with fact-based, nonpartisan information that can help improve federal government performance and ensure accountability for the benefit of the American people. GAO launched its WatchBlog in January, 2014, as part of its continuing effort to reach its audiences—Congress and the American people—where they are currently looking for information.
The blog format allows GAO to provide a little more context about its work than it can offer on its other social media platforms. Posts will tie GAO work to current events and the news; show how GAO’s work is affecting agencies or legislation; highlight reports, testimonies, and issue areas where GAO does work; and provide information about GAO itself, among other things.
Please send any feedback on GAO's WatchBlog to blog@gao.gov.